图书介绍
切削加工【2025|PDF|Epub|mobi|kindle电子书版本百度云盘下载】
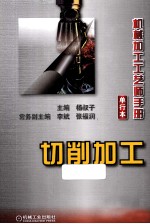
- 杨叔子主编;常治斌,鲍剑斌,汤漾平等副主编 著
- 出版社: 北京:机械工业出版社
- ISBN:9787111380320
- 出版时间:2012
- 标注页数:1158页
- 文件大小:230MB
- 文件页数:1173页
- 主题词:金属切削-生产工艺-技术手册
PDF下载
下载说明
切削加工PDF格式电子书版下载
下载的文件为RAR压缩包。需要使用解压软件进行解压得到PDF格式图书。建议使用BT下载工具Free Download Manager进行下载,简称FDM(免费,没有广告,支持多平台)。本站资源全部打包为BT种子。所以需要使用专业的BT下载软件进行下载。如BitComet qBittorrent uTorrent等BT下载工具。迅雷目前由于本站不是热门资源。不推荐使用!后期资源热门了。安装了迅雷也可以迅雷进行下载!
(文件页数 要大于 标注页数,上中下等多册电子书除外)
注意:本站所有压缩包均有解压码: 点击下载压缩包解压工具
图书目录
第3篇 切削加工3
第1章 车削3
1.1 车削基本特征与加工范围3
1.2 车削主要工艺参数4
1.2.1 各种车刀的切削用量4
1.2.2 车刀的磨钝标准与耐用度14
1.2.3 车削速度、车削力和车削功率14
1.3 车削精度31
1.3.1 车削加工的经济精度与表面粗糙度31
1.3.2 各种车床加工的质量问题与解决措施36
1.4 车床44
1.4.1 卧式车床44
1.4.2 立式车床48
1.4.3 转塔车床和回轮车床53
1.4.4 仿形车床61
1.4.5 卡盘多刀车床64
1.4.6 单轴自动车床67
1.4.7 多轴自动车床70
1.5 车刀73
1.5.1 车刀的类型与用途73
1.5.2 车刀的前面形状和几何参数74
1.5.3 断屑和卷屑75
1.5.4 硬质合金焊接车刀79
1.5.5 机械夹固式车刀80
1.5.6 硬质合金可转位车刀81
1.5.7 陶瓷、金刚石和立方氮化硼车刀105
1.5.8 成形车刀106
第2章 钻削、扩削、铰削109
2.1 钻、扩、铰的特点及主要工艺参数109
2.1.1 钻、扩、铰的特点109
2.1.2 钻头、扩孔钻和铰刀的磨钝标准及耐用度110
2.1.3 钻、扩、铰的切削用量、切削力和切削功率110
2.2 钻、扩、铰加工机动时间的计算159
2.3 钻、扩、铰的加工精度161
2.4 钻、扩、铰加工中常见问题的产生原因和解决方法162
2.5 深孔、小孔和微孔的钻削169
2.5.1 深孔钻削169
2.5.2 小孔和微孔的钻削170
2.6 钻床171
2.6.1 钻床的类型及适用范围171
2.6.2 台式钻床172
2.6.3 立式钻床172
2.6.4 摇臂钻床172
2.6.5 深孔钻床176
2.6.6 数控钻床和钻削中心179
2.7 孔加工刀具182
2.7.1 孔加工刀具的类型与用途182
2.7.2 麻花钻182
2.7.3 硬质合金浅孔钻197
2.7.4 扩孔钻和锪钻198
2.7.5 铰刀210
2.7.6 中心钻和扁钻228
2.7.7 深孔钻231
第3章 镗削242
3.1 镗削的特点与类型242
3.1.1 镗削的特点242
3.1.2 镗削类型及适用范围242
3.2 卧式镗床镗削243
3.2.1 卧式镗床的工作范围243
3.2.2 卧式镗床镗削时工件的定位方式243
3.2.3 卧式镗床镗削时工件工艺基准面的找正方法245
3.2.4 箱体类零件的镗孔方案247
3.3 金刚镗床镗削(高速精镗)247
3.3.1 金刚镗床镗削的特点247
3.3.2 金刚镗床加工中应注意的问题248
3.4 坐标镗床镗削251
3.4.1 加工前的坐标换算与调整251
3.4.2 坐标镗床的找正与测量252
3.4.3 镗削空间斜孔时的角度计算255
3.5 镗削用量256
3.6 镗削精度259
3.6.1 镗床的加工精度259
3.6.2 影响镗削加工质量的因素与解决措施260
3.6.3 提高镗孔精度的常用方法264
3.7 典型表面和零件的镗削264
3.7.1 同轴孔的镗削264
3.7.2 大孔和长孔的镗削265
3.7.3 阶梯孔和盲孔镗削266
3.7.4 小孔镗削267
3.7.5 内、外球面的镗削268
3.7.6 铣镗床立柱底面的镗削269
3.8 镗床269
3.8.1 卧式铣镗床269
3.8.2 坐标镗床275
3.8.3 精镗床278
3.8.4 深孔镗床和深孔钻镗床278
3.9 镗刀284
3.9.1 单刃镗刀284
3.9.2 多刃镗刀286
3.9.3 微调镗刀287
3.9.4 复合镗刀287
第4章 铣削289
4.1 铣削特点、方式及加工范围289
4.1.1 铣削特点289
4.1.2 铣削方式289
4.1.3 铣削精度和铣削效率290
4.1.4 铣削加工的应用范围297
4.2 铣削用量300
4.2.1 铣削要素300
4.2.2 铣削进给量300
4.2.3 铣削速度、铣削力及铣削功率的计算303
4.2.4 确定铣削用量和铣削功率的常用表格305
4.3 提高铣削精度和铣削效率的方法335
4.3.1 精铣335
4.3.2 高效铣刀铣削338
4.3.3 组合铣刀铣削339
4.4 典型零件和表面的铣削加工341
4.4.1 铣削花键轴341
4.4.2 铣削长齿条341
4.4.3 铣削凸轮343
4.4.4 铣削曲面345
4.4.5 铣削空间斜面346
4.5 铣削发展趋势348
4.6 铣床348
4.6.1 升降台铣床351
4.6.2 工具铣床、摇臂铣床和滑枕铣床351
4.6.3 床身式铣床351
4.6.4 龙门铣床和数控龙门镗铣床351
4.6.5 仿形铣床和数控仿形铣床360
4.7 铣刀371
4.7.1 铣刀的类型与用途371
4.7.2 高速钢尖齿铣刀371
4.7.3 高速钢铲齿铣刀389
4.7.4 套式铣刀391
4.7.5 硬质合金铣刀393
第5章 刨削、插削、锯削415
5.1 刨削415
5.1.1 刨削特点415
5.1.2 刨削用量415
5.1.3 刨削加工精度423
5.1.4 提高刨削效率的主要方法426
5.1.5 典型表面和零件的刨削加工429
5.2 插削435
5.2.1 插削的特点435
5.2.2 插削用量435
5.2.3 典型表面和零件的插削437
5.3 锯削441
5.3.1 锯削的特点441
5.3.2 锯削用量、锯削速度和材料切除率441
5.3.3 锯削加工精度与锯削中常见问题的解决方法445
5.4 刨床、插床和锯床447
5.4.1 刨床和插床447
5.4.2 锯床447
5.5 刨刀和插刀459
5.5.1 刨刀的类型与用途459
5.5.2 刨刀合理几何参数460
5.5.3 先进刨刀460
5.5.4 插刀的类型与选用467
5.5.5 插刀主要几何角度的选择468
第6章 拉削469
6.1 拉削的特点、类型及方式469
6.1.1 拉削的特点469
6.1.2 拉削的类型469
6.1.3 拉削的方式471
6.2 拉削用量、拉削力和拉削机动时间472
6.2.1 拉削速度的分组与选用472
6.2.2 拉削进给量474
6.2.3 拉削力474
6.2.4 拉削机动时间476
6.3 拉削切削液及其浇注方法476
6.3.1 常用拉削切削液476
6.3.2 切削液的浇注方法477
6.4 拉削中常见缺陷的分析与解决方法477
6.5 典型表面和零件的拉削加工479
6.5.1 对拉削工件的工艺要求479
6.5.2 汽车发动机轴瓦内圆表面拉削479
6.5.3 循环球转向机螺母滚道的螺旋拉削480
6.5.4 套管叉花键孔拉削480
6.5.5 齿条拉削480
6.5.6 渐开线凸轮轴拉削482
6.6 拉床482
6.6.1 拉床的类型及适用范围482
6.6.2 立式拉床485
6.6.3 卧式拉床485
6.6.4 连续拉床485
6.6.5 拉床发展趋势485
6.7 拉刀487
6.7.1 拉刀的类型487
6.7.2 拉刀的结构和几何参数487
6.7.3 拉刀的使用491
第7章 磨削492
7.1 磨削原理492
7.1.1 磨削过程与切屑的形成492
7.1.2 磨削基本参数492
7.1.3 磨削力和磨削功率494
7.1.4 磨削热和磨削温度496
7.2 磨削的基本特征和磨削类型497
7.2.1 磨削加工特点497
7.2.2 磨削分类497
7.2.3 磨削的经济加工能力498
7.3 普通磨削用量的选择498
7.3.1 砂轮速度的选择498
7.3.2 工件速度的选择499
7.3.3 纵向进给量的选择499
7.3.4 背吃刀量ap的选择499
7.3.5 光磨次数的选择499
7.4 常见磨削方式的主要工艺参数499
7.4.1 外圆磨削499
7.4.2 内圆磨削505
7.4.3 平面磨削512
7.4.4 无心磨削517
7.4.5 成形磨削521
7.5 砂轮的修整526
7.5.1 车削法修整526
7.5.2 滚压法修整528
7.5.3 磨削法修整529
7.5.4 修整砂轮注意事项529
7.5.5 超硬磨料砂轮的修整529
7.6 磨削液530
7.6.1 磨削液的种类530
7.6.2 磨削液的选用530
7.6.3 磨削液的过滤535
7.7 磨削常见缺陷的原因536
7.8 高效磨削539
7.8.1 高速磨削539
7.8.2 深切缓进给磨削540
7.8.3 连续修整深切缓进给磨削541
7.8.4 宽砂轮与多砂轮磨削542
7.8.5 恒压力磨削543
7.8.6 高速深切快进给磨削543
7.8.7 砂带磨削544
7.9 磨床553
7.9.1 概述553
7.9.2 外圆磨床553
7.9.3 内圆磨床564
7.9.4 平面磨床572
7.9.5 专门化磨床591
7.9.6 其他磨床599
7.9.7 数控磨床611
7.10 磨料磨具的选择618
7.10.1 普通磨料磨具的选择618
7.10.2 超硬磨料磨具的选择624
7.10.3 涂覆磨具的选择628
第8章 齿轮、蜗杆副、花键加工633
8.1 圆柱齿轮加工633
8.1.1 圆柱齿轮加工方法与工艺设计633
8.1.2 滚齿641
8.1.3 插齿662
8.1.4 剃齿671
8.1.5 珩齿679
8.1.6 磨齿687
8.1.7 冷挤齿691
8.1.8 轮齿端倒角693
8.1.9 重载齿轮加工工艺695
8.1.10 齿轮加工CAPP710
8.2 锥齿轮加工723
8.2.1 概述723
8.2.2 直齿锥齿轮加工734
8.2.3 曲线齿锥齿轮切齿方法741
8.2.4 锥齿轮研齿757
8.2.5 锥齿轮检验及接触区修正759
8.3 蜗杆副加工765
8.3.1 蜗轮加工特点与主要工艺参数765
8.3.2 蜗杆加工特点与主要工艺参数772
8.3.3 特殊蜗杆副加工779
8.4 花键加工781
8.4.1 花键加工的特点781
8.4.2 花键加工的主要方法784
8.5 齿轮加工机床822
8.5.1 概述822
8.5.2 滚齿机823
8.5.3 插齿机832
8.5.4 剃齿机836
8.5.5 珩齿机839
8.5.6 磨齿机839
8.5.7 花键轴铣床846
8.5.8 数控齿轮加工机床851
8.5.9 锥齿轮加工机床855
8.6 齿轮刀具868
8.6.1 齿轮铣刀868
8.6.2 齿轮滚刀871
8.6.3 插齿刀877
8.6.4 剃齿刀888
8.6.5 蜗轮刀具894
8.6.6 锥齿轮刀具898
8.6.7 非渐开线展成刀具919
第9章 螺纹加工927
9.1 螺纹加工的基本类型、特点及适用范围927
9.2 丝锥攻螺纹、板牙套螺纹930
9.2.1 普通螺纹丝锥攻螺纹930
9.2.2 锥形丝锥攻螺纹934
9.2.3 板牙套螺纹935
9.3 螺纹车削936
9.3.1 螺纹的车削特点与加工方式936
9.3.2 螺纹车削工艺参数939
9.3.3 螺纹切削的切削液选择940
9.3.4 精车精密丝杠的工艺要点941
9.3.5 螺纹车削时易产生的缺陷及改进措施942
9.4 螺纹磨削943
9.4.1 螺纹磨削的加工方式、特点及应用943
9.4.2 磨削用量的选择945
9.4.3 滚珠丝杠圆弧形螺纹磨削945
9.4.4 螺纹磨削的注意事项946
9.4.5 螺纹磨削常见缺陷及预防措施946
9.5 螺纹加工机床948
9.5.1 螺纹车床948
9.5.2 螺纹铣床948
9.5.3 螺纹磨床949
9.5.4 攻丝机949
9.5.5 滚丝机949
9.5.6 搓丝机951
9.6 螺纹刀具952
9.6.1 螺纹刀具的类型和用途952
9.6.2 螺纹车刀和梳刀952
9.6.3 丝锥954
9.6.4 板牙972
9.6.5 螺纹铣刀977
9.6.6 螺纹切头980
9.6.7 螺纹滚压工具988
第10章 精整和光整加工999
10.1 珩磨999
10.1.1 珩磨加工的原理和特点999
10.1.2 珩磨头及珩磨油石的选用999
10.1.3 珩磨主要工艺参数1006
10.1.4 珩磨加工技术的发展1011
10.2 研磨1012
10.2.1 研磨加工的特点与经济精度1012
10.2.2 研磨机理与运动轨迹1013
10.2.3 研磨剂和研具的选用1014
10.2.4 研磨主要工艺参数1020
10.2.5 典型零件的研磨加工1021
10.2.6 常见研磨故障及排除方法1023
10.3 抛光1025
10.3.1 概述1025
10.3.2 固结磨料柔性磨具抛光1026
10.3.3 自由磨料抛光1027
第11章 精密和超精密加工1037
11.1 概述1037
11.1.1 精密和超精密加工的范畴1037
11.1.2 精密和超精密加工的工作环境1037
11.1.3 精密和超精密加工的工件材料1038
11.1.4 常用的精密和超精密加工方法1039
11.2 金刚石刀具超精密切削1041
11.2.1 金刚石刀具超精密切削机理1041
11.2.2 金刚石车刀的设计和刃磨1042
11.2.3 金刚石刀具超精密车削工艺特点1045
11.2.4 超精密车削的发展趋势1046
11.3 精密和超精密磨削1047
11.3.1 精密和超精密磨削机理1047
11.3.2 精密磨削工艺参数1047
11.3.3 超精密磨削工艺参数1056
11.4 精密磨削实例1057
11.4.1 外圆精密磨削实例1057
11.4.2 内圆精密磨削实例1058
11.4.3 平面精密磨削实例1059
第12章 难加工材料的切削加工1060
12.1 难加工材料的切削特点1060
12.1.1 难加工材料的分类1060
12.1.2 难加工材料的切削加工特点1060
12.2 高强度钢的切削加工1060
12.3 高锰钢的切削加工1061
12.4 淬硬钢、冷硬铸铁及耐磨合金铸铁的切削加工1062
12.5 不锈钢、高温合金的切削加工1062
12.5.1 不锈钢、高温合金的切削加工特点1062
12.5.2 不锈钢、高温合金的车(镗)削加工1063
12.5.3 不锈钢、高温合金的铣削加工1066
12.5.4 不锈钢、高温合金的钻削加工1067
12.6 工程陶瓷的切削加工1070
12.6.1 工程陶瓷材料的特性1070
12.6.2 陶瓷材料脆性破坏机理1070
12.6.3 几种工程陶瓷材料的切削加工1070
12.6.4 陶瓷材料的离子束加热切削1072
12.6.5 陶瓷材料的磨削加工1072
12.7 其他难切材料的切削加工1072
12.7.1 石材的切削加工1072
12.7.2 复合材料的切削加工1073
12.7.3 工程塑料的切削加工1076
12.8 非金属材料加工用刀具1077
12.8.1 木材加工刀具1077
12.8.2 塑料加工刀具1093
12.8.3 石材锯切设备及刀具1103
第13章 高速切削加工1106
13.1 高速切削概述1106
13.1.1 高速切削的速度范围1106
13.1.2 高速切削的优越性1107
13.1.3 高速切削的切削力1107
13.1.4 高速切削的切削热和切削温度1107
13.1.5 高速切削的振动1108
13.1.6 高速切削时刀具的摩擦、磨损特征1109
13.1.7 高速切削的表面质量1110
13.2 高速切削刀具1112
13.2.1 高速切削刀具材料1112
13.2.2 高速切削可转位刀片1123
13.2.3 几种高速切削刀具1129
13.2.4 高速切削刀柄系统1133
13.3 高速切削机床1136
13.3.1 高速切削加工机床的要求1136
13.3.2 高速加工机床1136
13.3.3 高速加工机床构造特征1137
13.3.4 高速加工机床的控制系统1145
13.3.5 高速加工机床的合理选择1146
13.3.6 高速切削加工机床夹具的特点1147
13.4 高速切削的应用1147
13.4.1 铝合金的高速切削1147
13.4.2 铸铁与钢的高速切削1149
13.5 高速切削的安全性1152
13.5.1 高速切削的安全性要求1152
13.5.2 高速切削刀具系统的平衡1153
参考文献1154
热门推荐
- 3744947.html
- 121160.html
- 3706892.html
- 2493737.html
- 3340647.html
- 2719731.html
- 3751824.html
- 3037580.html
- 365649.html
- 219933.html
- http://www.ickdjs.cc/book_910207.html
- http://www.ickdjs.cc/book_3312878.html
- http://www.ickdjs.cc/book_2621085.html
- http://www.ickdjs.cc/book_1605005.html
- http://www.ickdjs.cc/book_3784824.html
- http://www.ickdjs.cc/book_1334534.html
- http://www.ickdjs.cc/book_2871529.html
- http://www.ickdjs.cc/book_2442499.html
- http://www.ickdjs.cc/book_1649985.html
- http://www.ickdjs.cc/book_1063564.html